Service FAQs
Instantel offers calibration and repair services for all models of Instantel seismographs and sensors.
We recommend that your equipment return to Instantel annually for calibration. Each time your equipment is at Instantel for calibration, it is assessed to ensure it is working in accordance with industry guidelines and specifications. After each calibration is completed, a calibration certificate that conforms to international guidelines like the ISEE and DIN will be issued.
We drive quality in every service we deliver and never take shortcuts. We calibrate at every frequency on the spectrum, not just a subset. When your units are calibrated by Instantel, you can guarantee that your event data is accurate. Our Service and Calibration team is committed to low turnaround times, keeping units where they are needed – in the field.
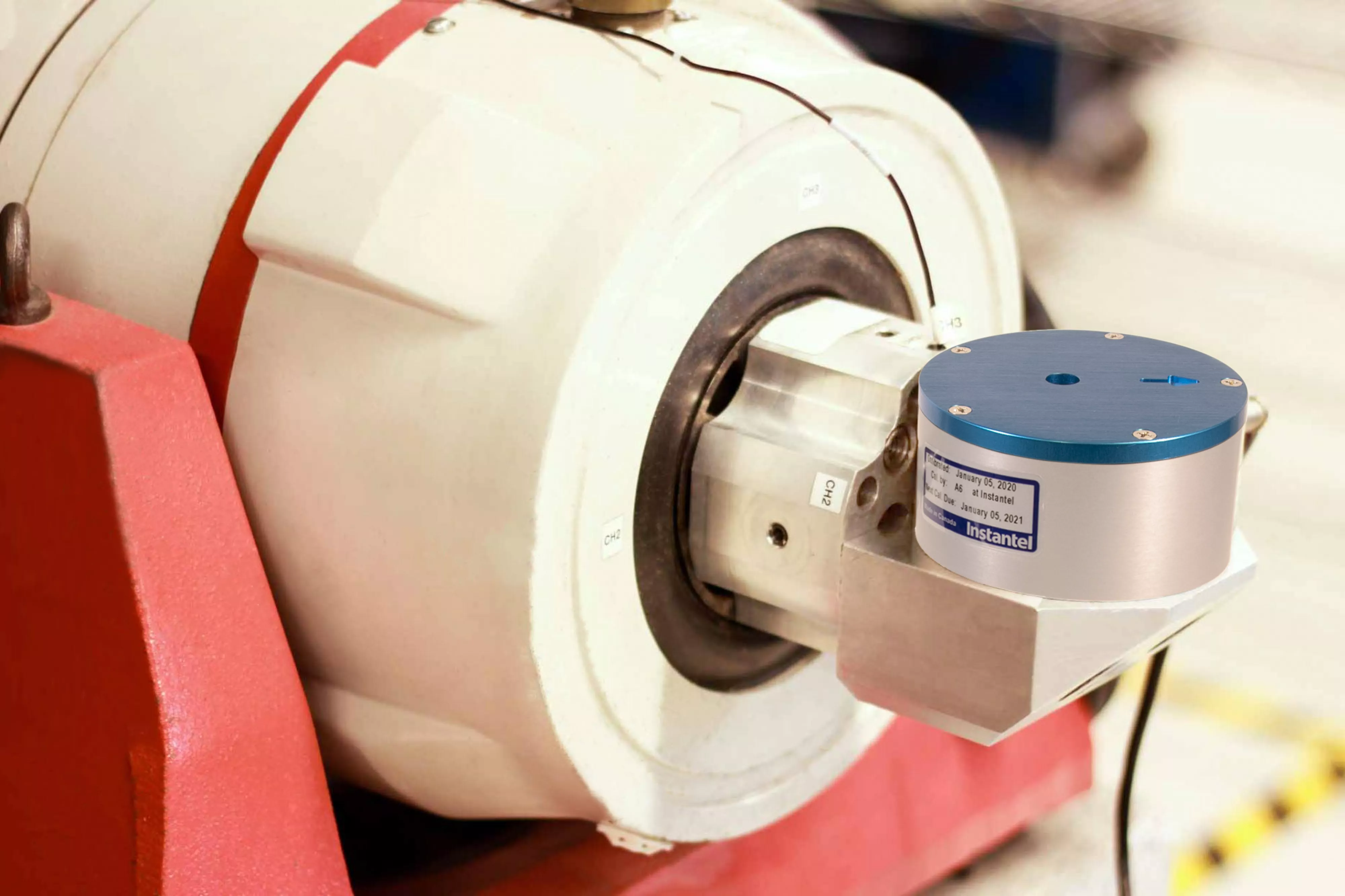
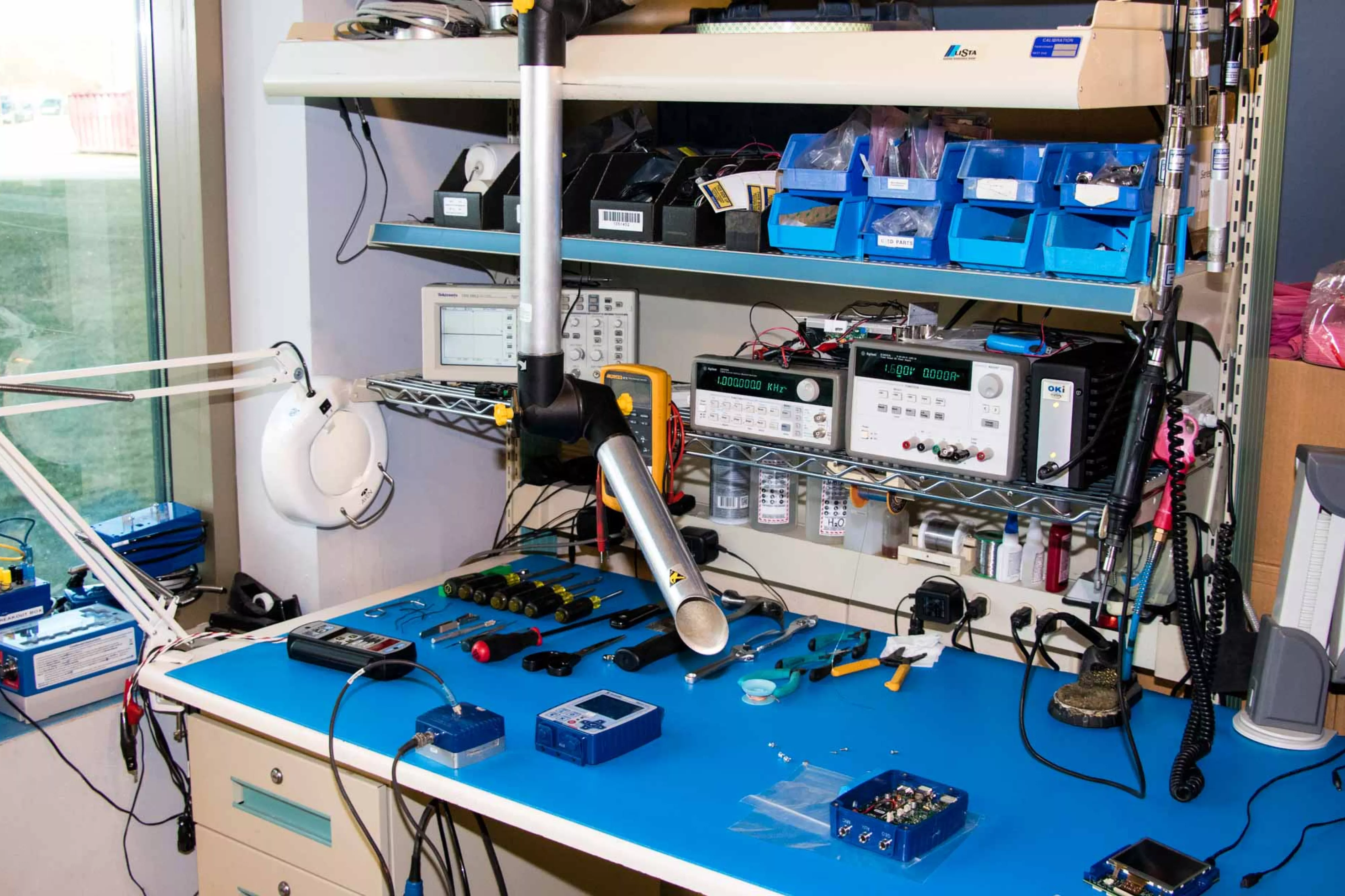
Although seismographs are designed for use in harsh environments, they are still a sophisticated piece of monitoring equipment. An accurate seismograph helps you prove that your vibration, air overpressure, or noise conforms to industry guidelines and regulations. Often, the accuracy of a seismograph is questioned in insurance claims and in the case of liability or property damages, so it is important that it is recording accurately.
Over time, the accuracy of your equipment degrades due to normal wear and tear. Oftentimes, extreme conditions or misuse can cause the accuracy to degrade more quickly. Calibration is important to ensure the seismograph is performing as it was designed to and is measuring accurately. Calibration is the comparison between a known measurement and the measurements recorded by your seismograph. An up-to-date calibration gives you and the governing regulatory body confidence in the measured results. It also includes preventative maintenance or repairs to the equipment.
A calibration certificate from Instantel provides you with proof that your seismograph is maintained, accurate, and functioning within specification.
Instantel recommends an annual calibration for all of our products, including seismographs, geophones, microphones, and accelerometers.
Across most of North America and many parts of Europe, regulatory authorities require seismographs to be calibrated on an annual basis. This requirement has been or is being adopted by several other countries around the world. The penalty for having an uncalibrated seismograph could delay project start times, loss of business, or financial penalties. In the end, the cost of not calibrating your seismograph could be much higher than the cost of the calibration.
To ensure the accuracy of the readings and to schedule any preventative maintenance, you should have your seismograph calibrated annually. You should also have your seismograph calibrated if it has experienced water or other significant damage, if it has experienced any mechanical or electrical shock, or if any of the internal sensors have been tampered with.
Should an authority question your measurement records, a Calibration Certificate is the document that provides proof of professional calibration. It also provides proof of the date that the calibration was completed.
When your seismograph is calibrated at Instantel, a Calibration Certificate that conforms to industry guidelines like the International Society of Explosive Engineers (ISEE 2022) is issued. This Calibration Certificate includes key elements such as:
- Name and address of the calibration facility
- Serial numbers of your tested equipment
- The model number and a description of your tested equipment
- Date the calibration was completed on
- A list of the equipment used to Perform the calibration and the standards they are traceable to
- An "As Found" report
- Graphical results of the calibration
- Name and signature of the technician
Certified Calibration using a manufacturer certified facility ensures that proper procedures are followed when calibrating your equipment. This removes any uncertainty associated with the reliability and measurement accuracy, and ensures the integrity of the measured record if it is ever called up as evidence in a court of law.
Calibration facilities that are certified by the manufacturer have access to test specifications and procedures designed specifically for your equipment. They will also ensure that any replacement parts that are used meet the specifications for the equipment. If your equipment requires repair, the manufacturer has the best experience and knowledge to diagnose and fix the problem.
It is in your best interest to have your monitor calibrated by the specific manufacturer or their authorized agents. There are individuals and companies worldwide that are not certified by the manufacturer to perform vibration monitor calibration, yet continue to do so. Using unauthorized facilities may cause problems in court.
No, a Sensor Check is not a calibration.
Sensor Checks do not compare the measured results against an external reference sensor, nor do they test the electronic circuits that are integral to the sensor’s response.
The Sensor Check is designed to provide information on the setup and installation of the sensors connected to your monitoring unit. Using the sensor check before you begin monitoring reduces error in the data that may be caused by an incorrectly installed or connected sensor. For example, if a standard geophone was not level, or was installed upside down, the Sensor Check would display a failed sensor.
A Sensor Check is a good indicator that the sensors and unit are working and installed properly. However, it is not a calibration check and does not replace the calibration process.
To better serve you, we require a few pieces of information to open your service request. We recommend having the information below available before you start your submission. The recommended information, such as the model and serial number, can be found on the Instantel product information sticker located on the outside of your Instantel equipment. Please see the image below for an example. If you have trouble locating this information, please email [email protected].
You will need the following information to submit a service request:
- Serial Number (Example: UM12345)
- Model (Example: Micromate)
- A Return Shipping Address
- Return Carrier Information – If you have a corporate shipping account with a carrier (UPS, Dicom, etc), please let us know. We would be happy to return your equipment using your preferred carrier. Otherwise, we will use one of our preferred carriers.
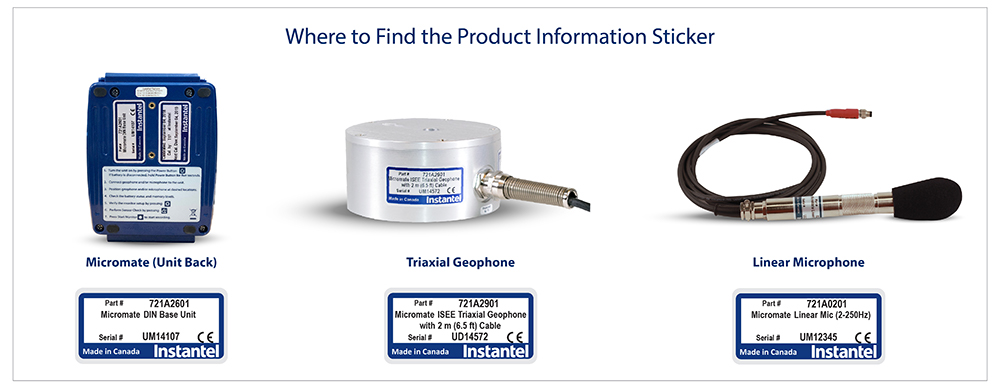
Please follow the instructions below to create a request for calibration or repair services on your Instantel equipment.
- Login to the Instantel Service Portal.
- Once you are logged in, click on Create RMA Request.
- You will then have to fill in your Contact Information, your Local Distributor's Contact Information, and the Return Shipping Address.
- Click Continue.
- Enter information about your Instantel equipment. There is also a section here to enter any details or items you would like our technicians to review.
- Click Continue.
- You will be provided with an RMA (Return Material Authorization) number – this is your service request number. An email with instructions on how to send your equipment to Instantel will be sent to the email address used to submit the request. This email will also include a return shipping label with Instantel’s corporate address and the RMA number.
- Please use the shipping labels provided to return your equipment to Instantel.
Please follow the instructions attached here to create a multi unit calibration or repair services request for your Instantel equipment.
Please follow the instructions below to check the status of an existing Instantel calibration or repair request.
- On the Instantel website, click on the "Schedule Service" button at the top right.
- If you have an existing service account, log in. If not, please click Create New Account to create one. Please remember this login information for future service requests. Note: Username and password are case-sensitive.
- Click View RMAs.
- You will be provided with a list of RMAs that were opened under your account. This list will tell you the RMA number, serial number, the date you submitted the RMA, the current state the RMA is in, and the date it was moved to its current state. Note: If you see On Hold or Quote Sent as the current state, please contact our Service Department for more information.
Instantel Service Process
Your equipment moves through a series of checkpoints, or states, throughout its time at Instantel. These checkpoints let us keep you informed every step of the way of the service process. As each checkpoint is reached, the current state column will be updated in real time.
Each RMA number is unique, and the checkpoints your equipment reaches while at Instantel will depend on the type of work required for the equipment. Below is a diagram showing a path of the checkpoints a service request can pass through while at Instantel. Please note that these checkpoints may change based on the technician’s findings. For example, a unit that was here for calibration may require repairs before the calibration can be completed.
If you have any questions on the status of your equipment, please email [email protected].
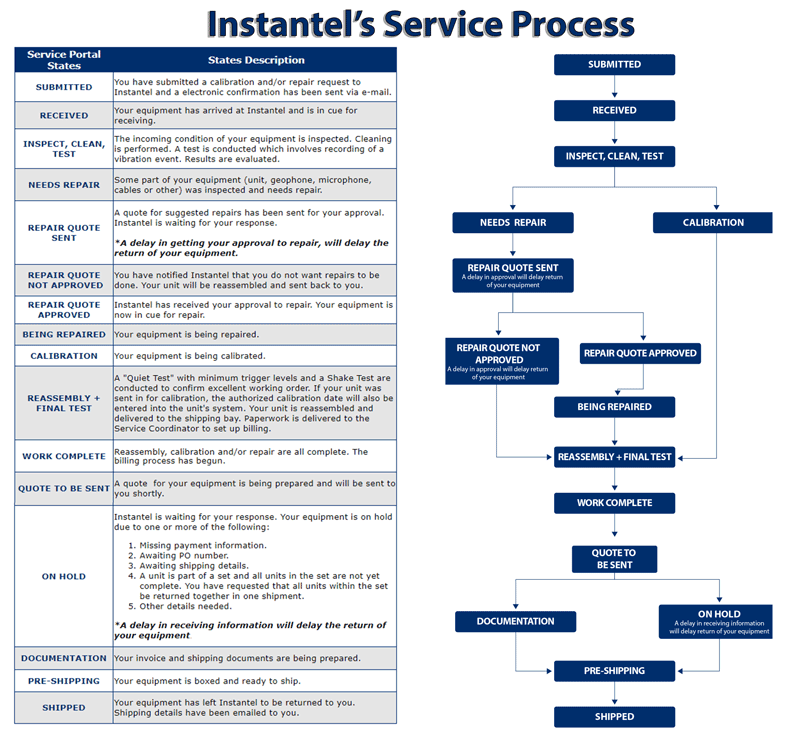
Instantel offers a limited services warranty of ninety (90) days. Download the warranty policy for all the details.